Exhaust pipe
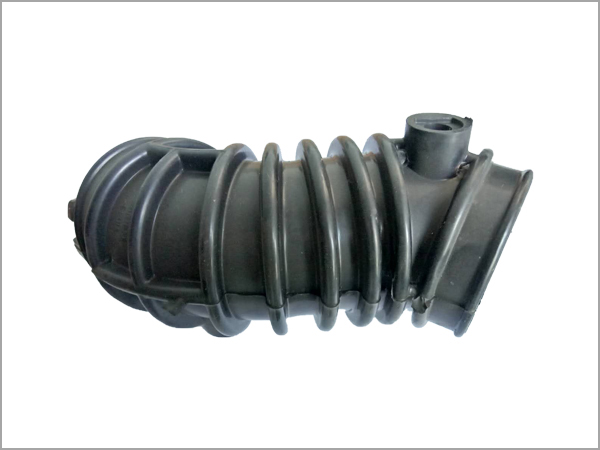
Chloroether rubber
Epichloro-hydrin rubber refers to a polyether rubber containing chlorine on its side groups. It is a polymeric elastomer obtained by ring-opening polymerization of a cyclic ether containing an epoxy group. It used to be called chlorine rubber. This rubber is classified into two types, a homopolymer and a copolymer, depending on the polymerization method. The former is made of epichlorohydrin alone. It is commonly used by CHR. It is named CO in China. The latter is made up of copolymerized epichlorohydrin and ethylene oxide. It is commonly used in CHC and is named ECO in China.
The chloroether rubber is insoluble in common solvents. Soluble in cyclohexanone, pyridine, chlorobenzene, nitrobenzene, tetrahydrofuran, dimethylformamide and the like. The performance is comprehensive, heat-resistant, ozone-resistant, wear-resistant, tear-resistant, and airtight than nitrile rubber and neoprene. Oil resistance and processing performance are better than EPDM rubber. Used in automotive parts, rubber rollers, fuel tanks, cable cladding, etc. It also has good adhesion to textile materials, metals and other rubbers and can be used as an adhesive.
The polyether polymer was studied as early as 1863 by Wurtz, when he polymerized ethylene oxide to produce a polymer. Staudinger not only systematically studied the polymerization of polymethylene oxide but also the polymerization of ethylene oxide, and reported the relationship between molecular weight and polymer properties. Although the polymerization of alkylene oxides has such a long history, it is rarely used industrially. It was not until 1955, when Pruitt and Baggett of Dow Chemical Company of the United States discovered an iron-based catalyst that a polymer of propylene oxide was produced. In 1959, the United States General Tire developed a zinc-based catalyst and then made a propylene oxide rubber (POR). In 1959, Vandenberg of Hercules Inc. of the United States produced an aluminum-based catalyst, which led to the activation of epichlorohydrin-based polymerization.
The industrial production of the chloroether rubber school began in 1965, the first production of the United States Goodrich and Hercules. At that time, the former was established in Ohio, USA (intermediate test workshop), respectively, the epichlorohydrin homopolymer (CHR or CO) under the trade name "Hydrin100", the equivalent of epichlorohydrin and ethylene oxide. Equimolar copolymers (CHC or ECO for short) are available under the trade name "Hydrin 200". Hercules, Inc., established a plant in Mississippi, USA, to promote the epichlorohydrin homopolymer and the copolymer of epichlorohydrin and ethylene oxide under the trade name "Herclar H" and the trade name "Herclor C". To the market.
In Japan and the United States, the industrialization of chloroether rubber was carried out at the same time. The Japanese company was producing the unsaturated copolymer containing allyl glycidyl ether at the company's Deshan plant while distributing the products of the two companies in the United States. . In 1979, due to the further increase in the demand for chloroether rubber in the automotive industry, Japan’s Reynolds, Osaka Alkali and Hercules jointly developed a development plan for chloroether rubber, which brought Japanese chloroether rubber into a new period.
Epichloro-hydrin rubber refers to a polyether rubber containing chlorine on its side groups. It is a polymeric elastomer obtained by ring-opening polymerization of a cyclic ether containing an epoxy group. It used to be called chlorine rubber. This rubber is classified into two types, a homopolymer and a copolymer, depending on the polymerization method. The former is made of epichlorohydrin alone. It is commonly used by CHR. It is named CO in China. The latter is made up of copolymerized epichlorohydrin and ethylene oxide. It is commonly used in CHC and is named ECO in China.
The chloroether rubber is insoluble in common solvents. Soluble in cyclohexanone, pyridine, chlorobenzene, nitrobenzene, tetrahydrofuran, dimethylformamide and the like. The performance is comprehensive, heat-resistant, ozone-resistant, wear-resistant, tear-resistant, and airtight than nitrile rubber and neoprene. Oil resistance and processing performance are better than EPDM rubber. Used in automotive parts, rubber rollers, fuel tanks, cable cladding, etc. It also has good adhesion to textile materials, metals and other rubbers and can be used as an adhesive.
The polyether polymer was studied as early as 1863 by Wurtz, when he polymerized ethylene oxide to produce a polymer. Staudinger not only systematically studied the polymerization of polymethylene oxide but also the polymerization of ethylene oxide, and reported the relationship between molecular weight and polymer properties. Although the polymerization of alkylene oxides has such a long history, it is rarely used industrially. It was not until 1955, when Pruitt and Baggett of Dow Chemical Company of the United States discovered an iron-based catalyst that a polymer of propylene oxide was produced. In 1959, the United States General Tire developed a zinc-based catalyst and then made a propylene oxide rubber (POR). In 1959, Vandenberg of Hercules Inc. of the United States produced an aluminum-based catalyst, which led to the activation of epichlorohydrin-based polymerization.
The industrial production of the chloroether rubber school began in 1965, the first production of the United States Goodrich and Hercules. At that time, the former was established in Ohio, USA (intermediate test workshop), respectively, the epichlorohydrin homopolymer (CHR or CO) under the trade name "Hydrin100", the equivalent of epichlorohydrin and ethylene oxide. Equimolar copolymers (CHC or ECO for short) are available under the trade name "Hydrin 200". Hercules, Inc., established a plant in Mississippi, USA, to promote the epichlorohydrin homopolymer and the copolymer of epichlorohydrin and ethylene oxide under the trade name "Herclar H" and the trade name "Herclor C". To the market.
In Japan and the United States, the industrialization of chloroether rubber was carried out at the same time. The Japanese company was producing the unsaturated copolymer containing allyl glycidyl ether at the company's Deshan plant while distributing the products of the two companies in the United States. . In 1979, due to the further increase in the demand for chloroether rubber in the automotive industry, Japan’s Reynolds, Osaka Alkali and Hercules jointly developed a development plan for chloroether rubber, which brought Japanese chloroether rubber into a new period.